SST LED Curing
Flexo Printing
What SST LED Curing Systems Offer?
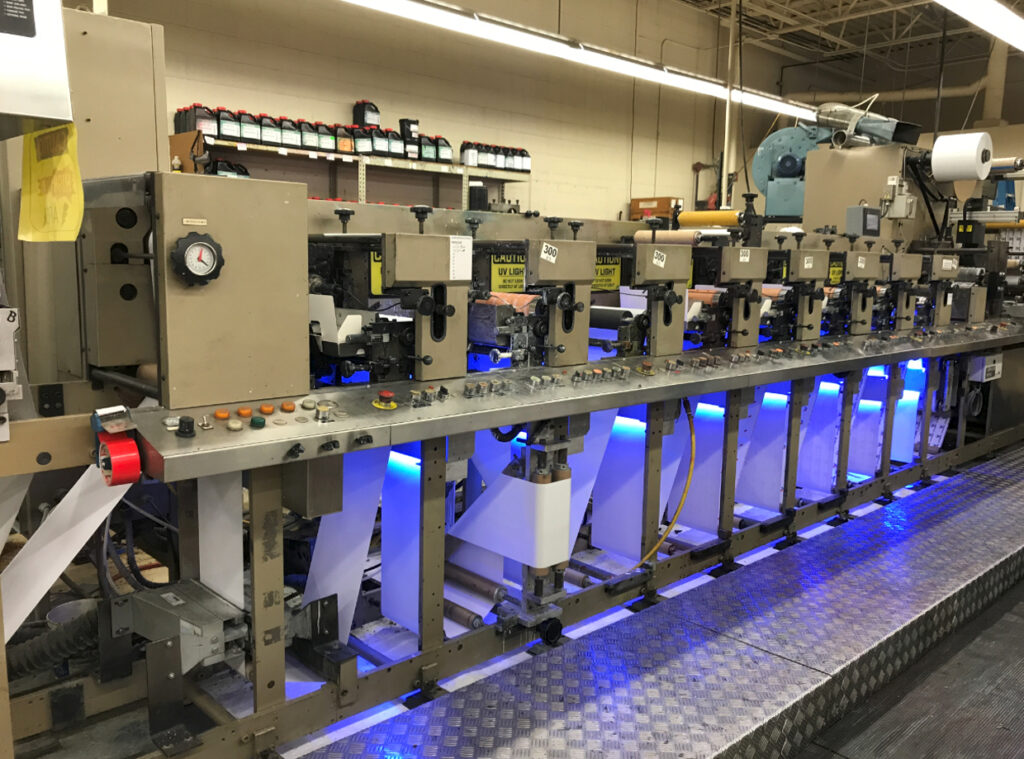
Up to 800ft/min
SST Water-cooled Standard LED Curing Lamps can print flexo up to 600 fpm. The SST ST80B168 series Water-cooled LED Curing lamps can be used for Flexo printing at speeds of over 800 ft/min.
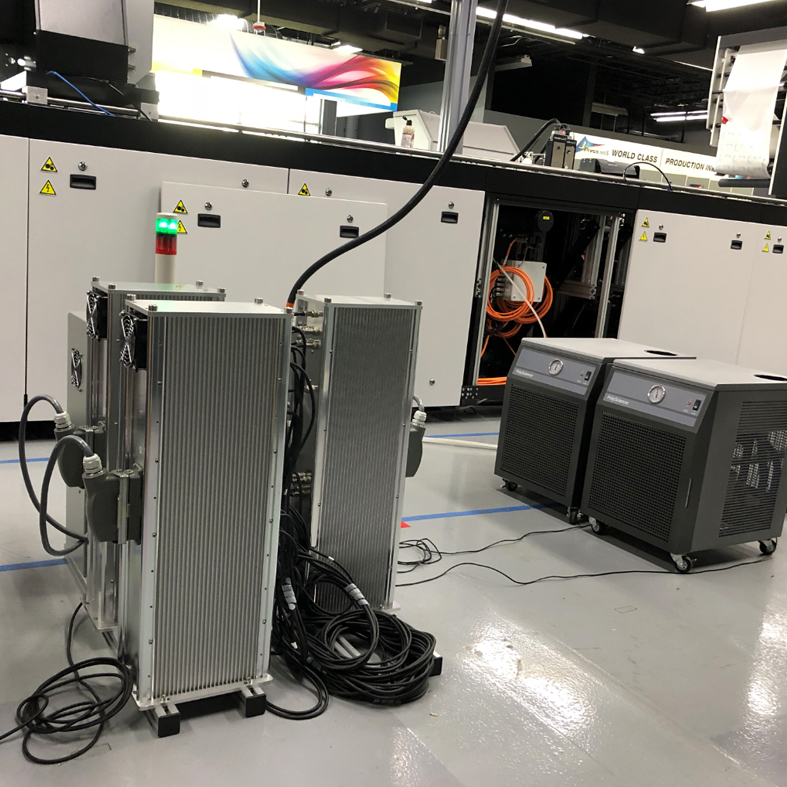
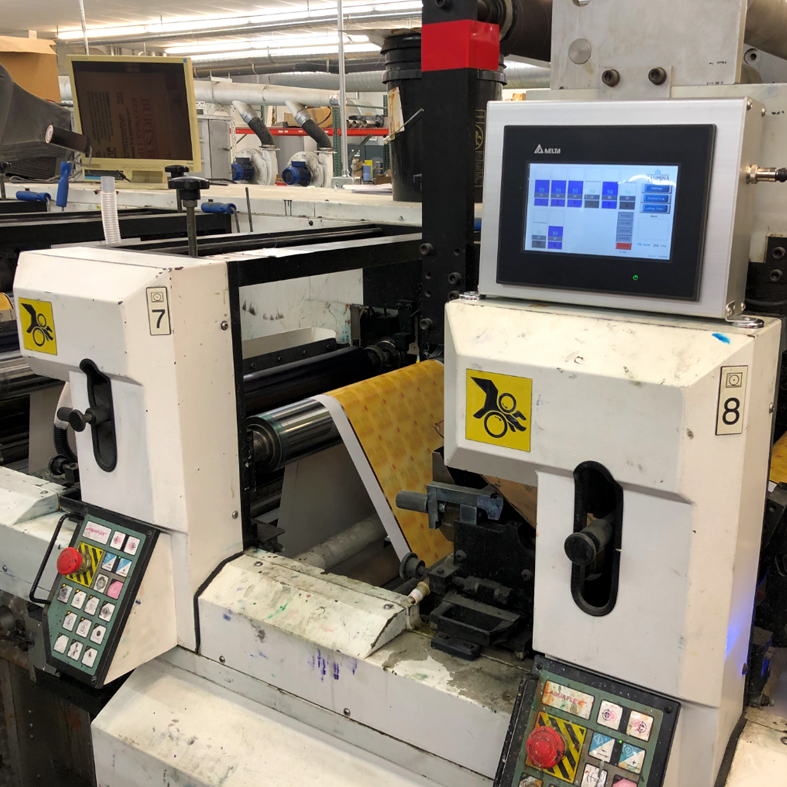
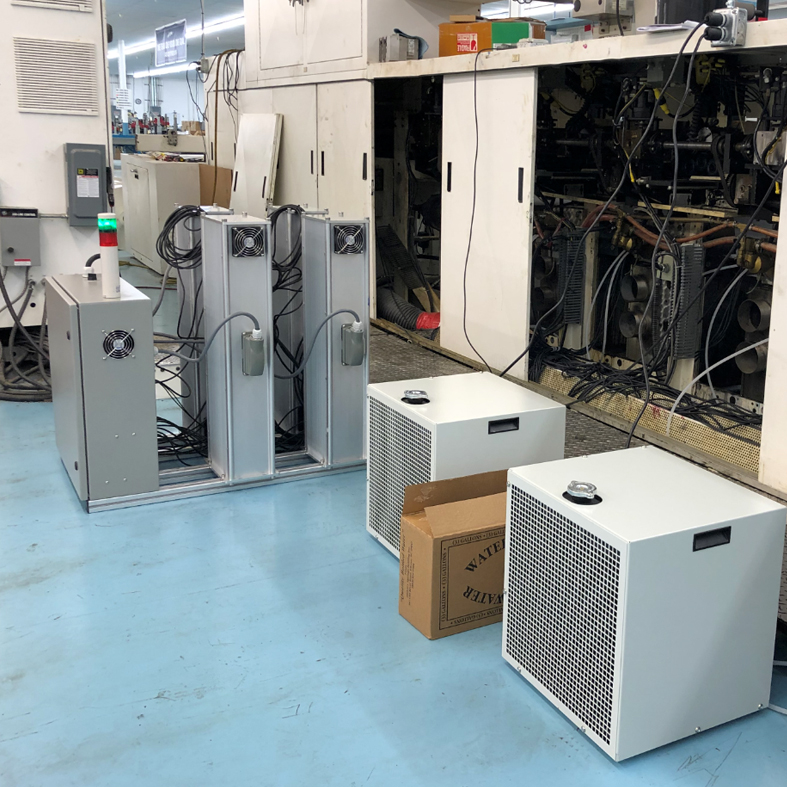
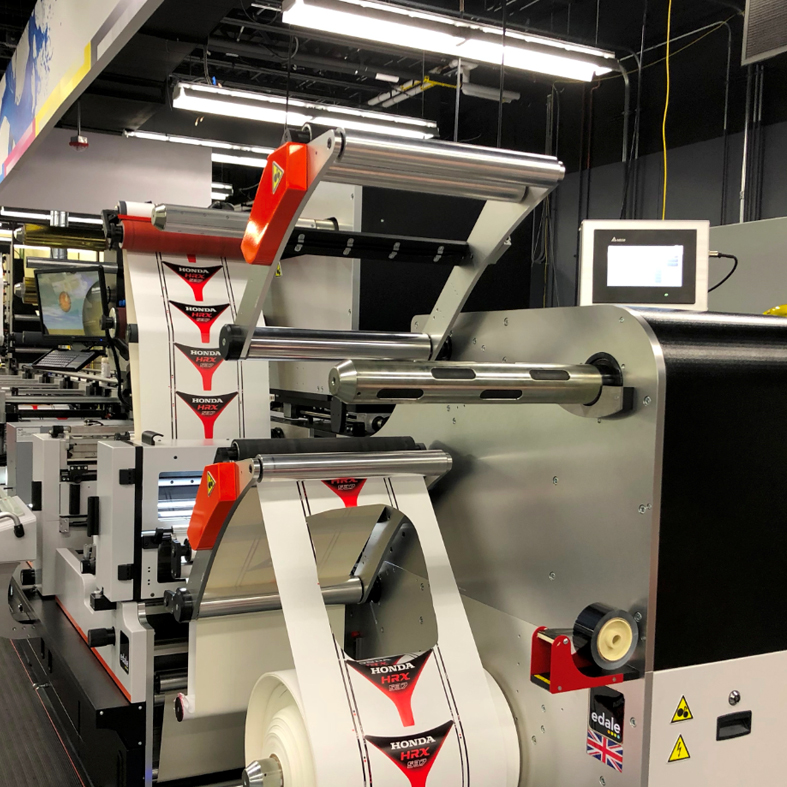
Key Features
- Touch screen allowing customizing power for each station
- Small room-temperature water-circulating system
- Automated power toggle feature to match printing process
- Instantaneous on/off
- Compact housing is easily placed close to the substrate (0.25 inches is recommended for most flexo applications) Standard 10”, 13”, 17”, 21″, 25″ or other custom width.
- Communication can be integrated into the press control through SST’s communication cables, or be controlled by SST’s central control box.
Other Features
- Simplest and fastest maintenance of any flexo technology
- Patented technology provides 30,000 hours chip life or 10+ years for 2 shift operation
- (Assumptions: 8 hours per shift, 70% printing time, 2 shifts per day, 5 shifts per yr, 50 weeks per year and 30,000 hours chip life)
- Lowest available energy consumption and carbon emmissions technology
- Environmentally friendly – eliminate voc’s and mercury
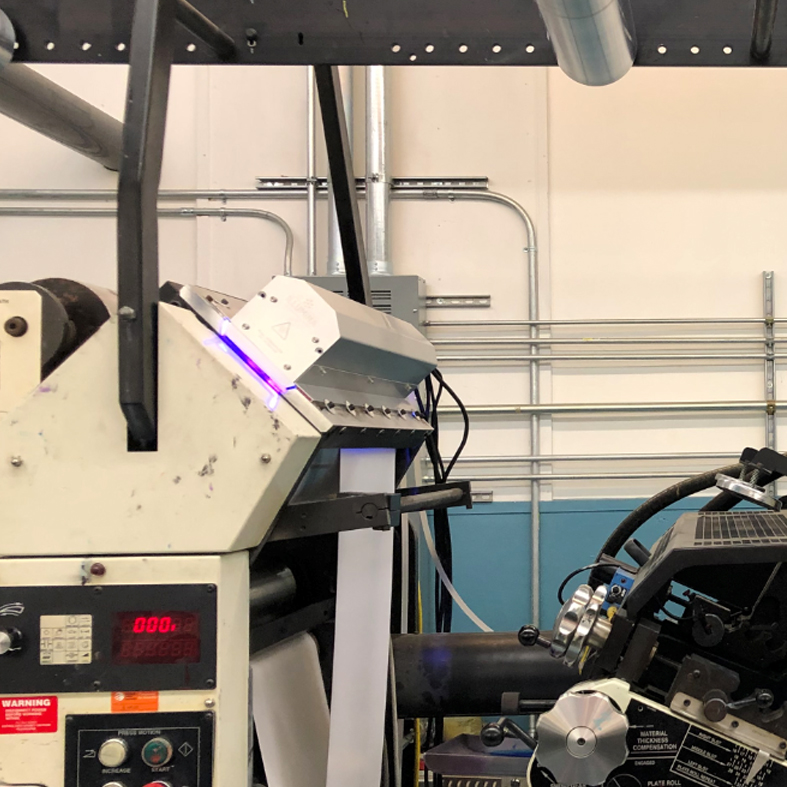
LED Retrofit System
SST UV LED converts any traditional UV or waterbase narrow web flexo press to UV-LED curing, typically in 8 to 12 hours.
By the second shift, you’ll be in production with the leading LED technology availble. The compact design of the SST LED cruing lamps easily fit on most any narrow web flexo press, at any width. The SST LED housing mounts directly on waterbase flexo presses without adding an extra drum as required by other LED retrofit systems.
The SST system is so compact it can typically be mounted redundant to the existing UV or waterbase system. This allows printers to convert quickly and risk free and later remove the old old systems and exhaust.
SST UV LED retrofit improves the run speed, especially for water-based flexo presses.
The retrofit SST LED curing system includes a central control box with main on/off switch to set the system ready to be powered, providing digital or analog control to the UV lamps. It can receive a UV run signal or 0-10V speed signal from the press, and is capable of sending a “UV ready” signal to the press. The control box also monitors lamp temperature and water re-circulator status. The LED indicator stick indicates the status of the system.
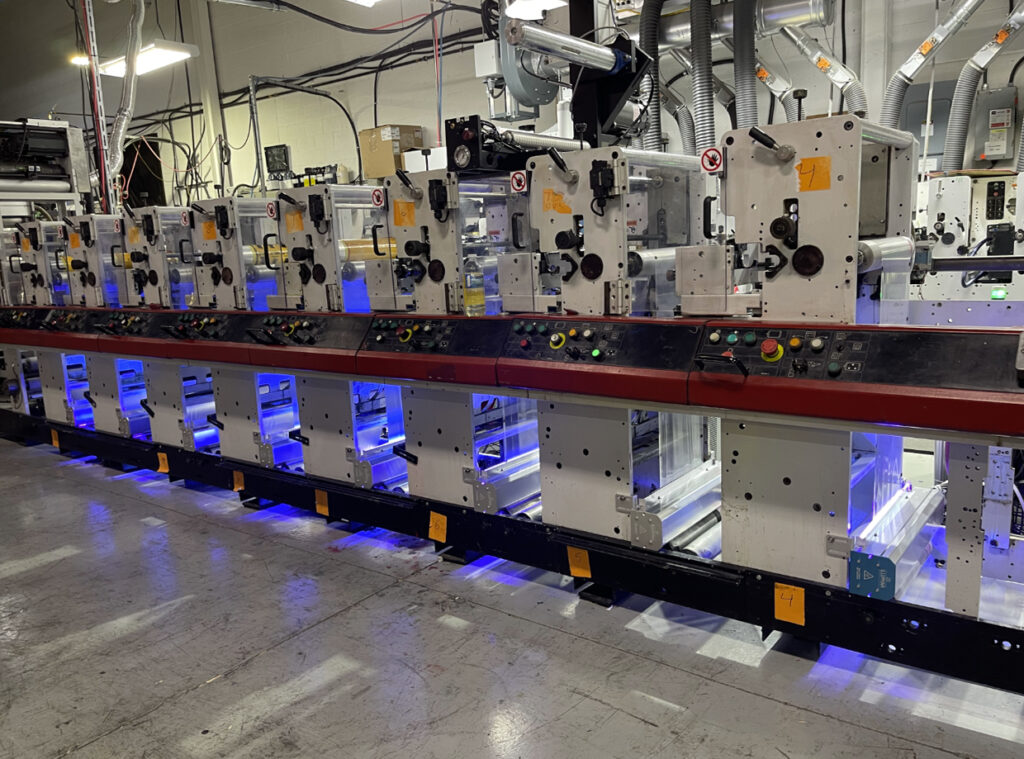
Heat-sensitive Film Market
Helps the printer to quickly enter the growing heat-sensitive film market without investing in chill drums and rollers .
The patented SST LED COLDCURE technology produces so little heat that it cures even the highest % shrink film WITH no chilling or chill drum rollers. This means you can literally begin printing shrink sleeves on a press without adding chilling equipment OR remove the chilling systems from an existing press. This delivers even more energy savings, less press downtime and significantly reduces maintance costs for the life of the press.
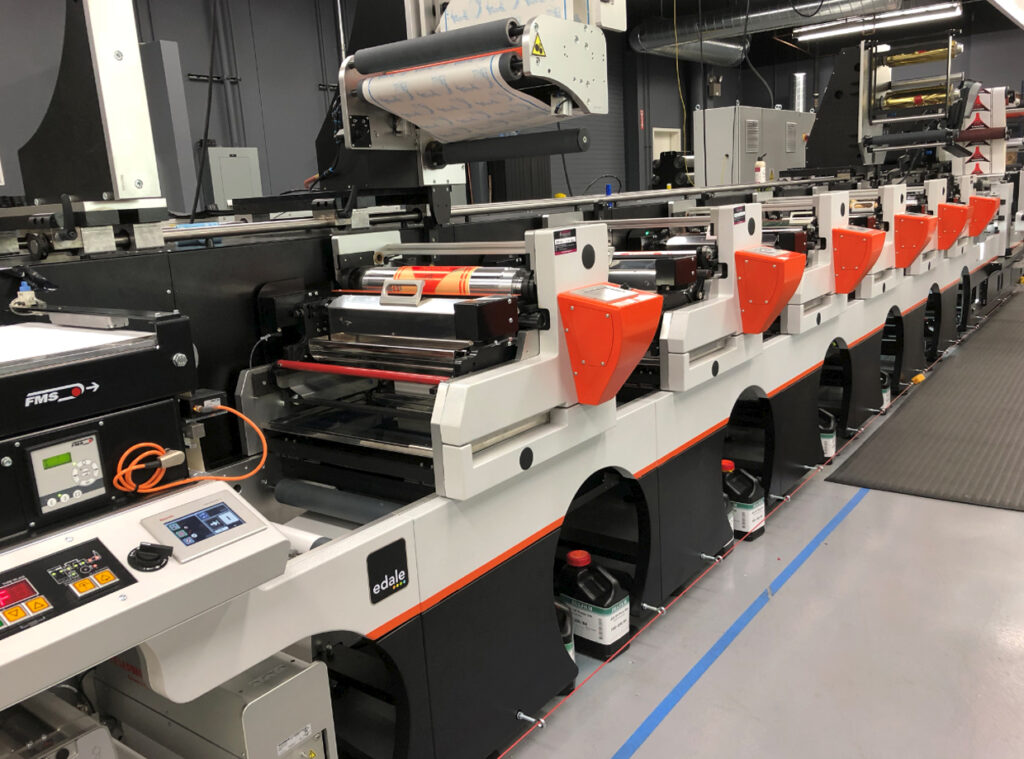
Integration onto New Press
SST have now collaborated with most major Narrow Web Flexo press manufacturers to seamlessly integrate the SST LED system onto new flexo and hybrid flexo presses.
This was initially driven by printers that had previously retrofit older preses to SST LED insisting the technology be included on new press purchases.
The COLDCURE technology enables new presses to no longer require chill drums and chilling systems which reduces the capital and maintenance cost as well as provides a smaller footprint on the pressroom floor and eliminates the need for new exhust systems and ducting.
RETROFIT CASE STUDY
The pictures below show the before and after equipment of a typical flexo press retrofit from UV to SST LED
This was a 2004 Aquaflex 8 station by 20” wide
The equipment on the left was completely replaced by the equipment on the right (38”L x 95”W x 35”H Power & water circulation units)
The retrofit took 1 normal shift to install.
The annual power consumption was reduced from 205,000 kwh to 17,400 kwh, they are still able to print shrink sleeves even though the chilling system has been removed.
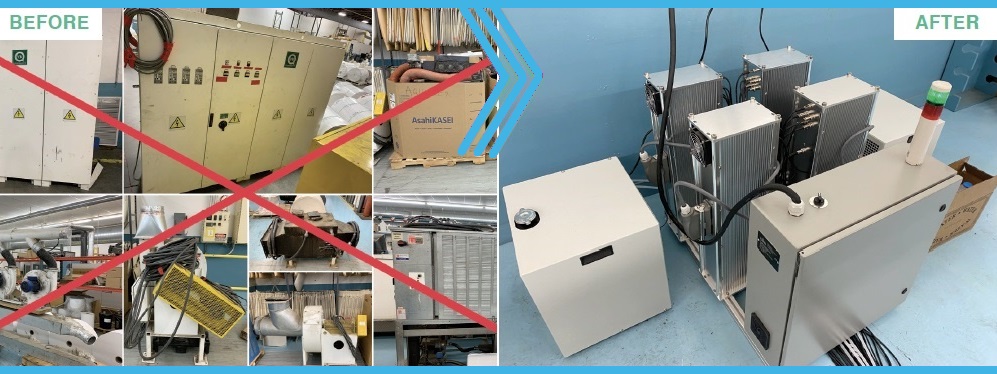