SST LED Curing
Proven disruptive Technology Transforming UV Screen Printing to LED
SCREEN PRINTING
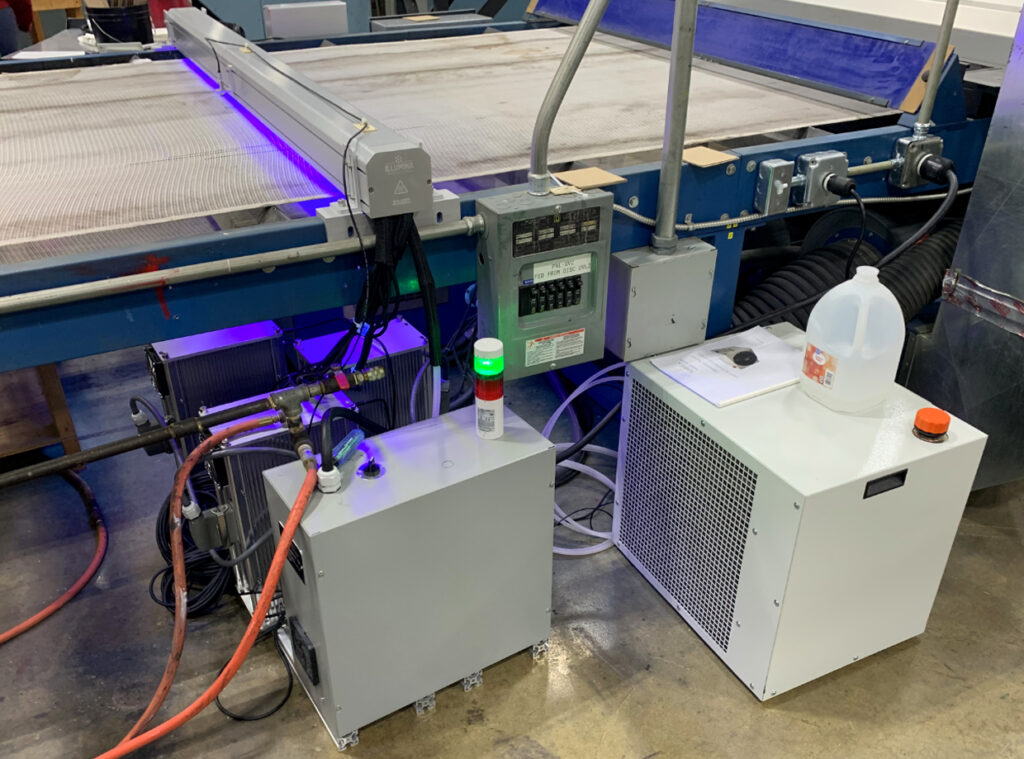
SST offers Pioneering Industry ColdCure Technology to Transform UV Screen Printing to LED
- Lowest available energy consumption and carbon emissions
- Fast payback on investment
- Eliminiates heat from printing proces
- Improve productivity and print quality
- Capatible with most common LED screen printing inks
- Simplifies the printing process
- Retrofit a press in 1/2 a day
- Optional paper detector
Eliminates Fires and Substrate Distortion
Eliminates Fire On Press
- Decrease press downtime
- Decrease subsrate, ink and labor waste
- Increase productivity/yieldBeginner- 2h 24m
Eliminates Substrate Distortion from UV Heat
- Faster and consistent registration
- Eliminate post print curling, mottling, or blocking due to heat
- improves die cutting varability due to heat.
Reduction in Maintenance Time and Cost
- No moving parts, refletor or shutters
- Bulb replacement at least 15X less often
- Less frequent maintenance
- less time per maitenance
Saves Energy and Space
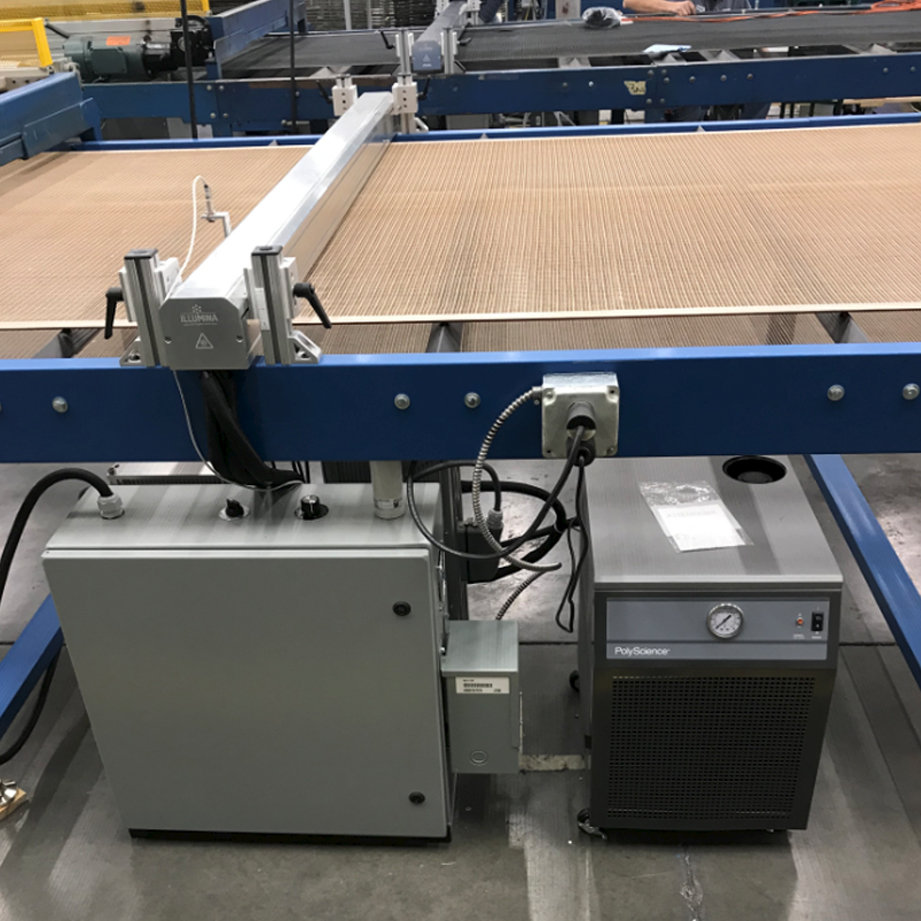
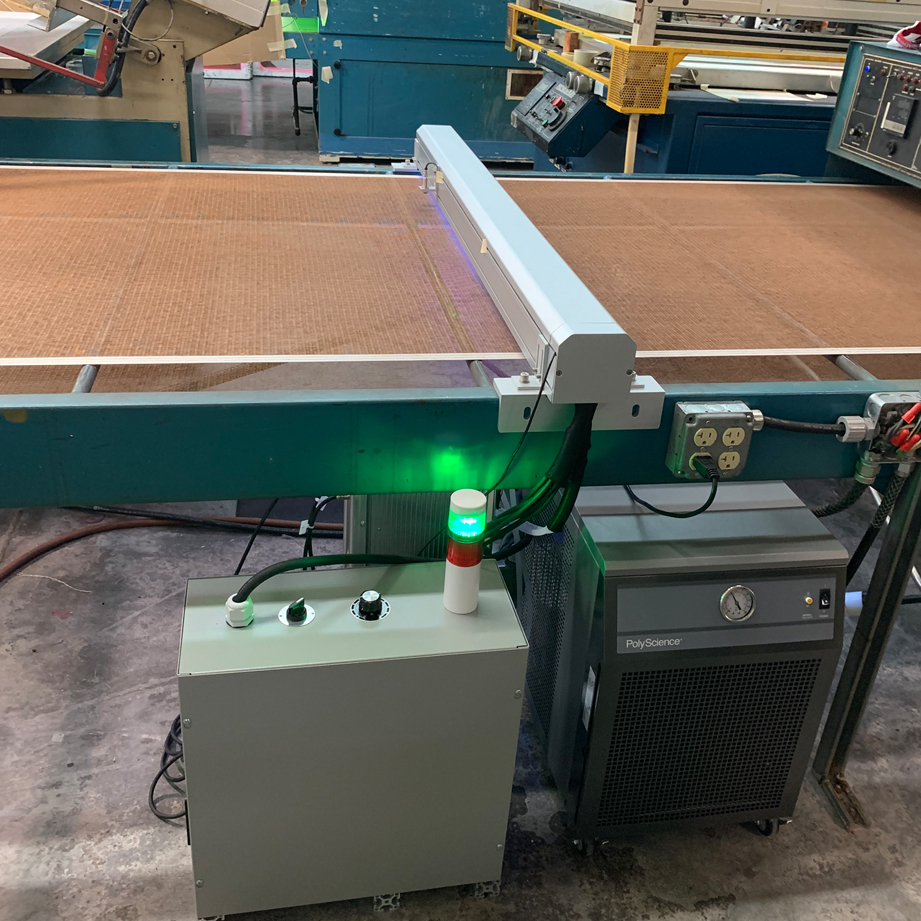
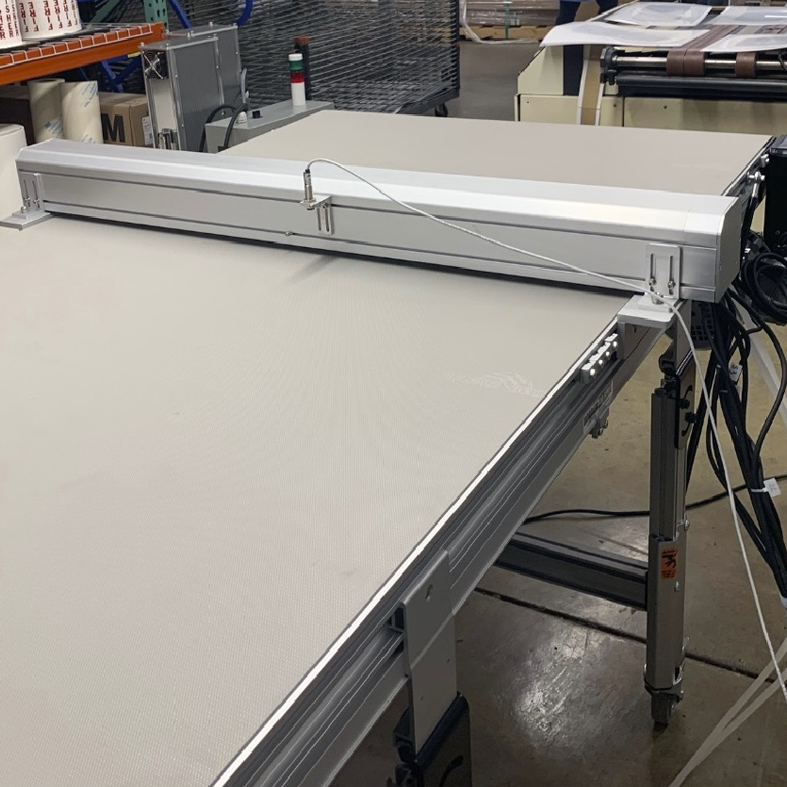
Energy cost and carbon emission reduction
- 90% reduction in curing systems
- 100% reduction in exhaust systems
- Reduction in air conditioning costs in print room
- Eliminate fans/cooling equipment cost in finished product stacks
- Supports sustaianability and green initiatives
- Eliminate VOCs and mercury
High dosage and dwell time deliver
- Faster curing time
- Improved adhesion
Scalable
- up to 120″
Others
- Eliminate need for roof penetration and maintenance of exhasut systems
- Eliminate air movment and dust from exhaust systems
- reduced sq. foortage requirement for curing and exhaust
- significant reduction in nloise in working environment
Lowest Energy Consumption, Converts in 1/2 day
The SST LED curing retrofit can be completed in a day or less and be ready immediately for ink and substrate testing. The SST LED curing Lamp System utilizes wider dose window with double irradiance peaks to achieve excellent cure with the lowest electricity consumption and heat development.
Heat Reduction extends the lifetime of LEDs
Heat is the primary cause of LED failure and degradation.
Saves Space
This sytem produces low heat and low air exchange, perfect for clean room use. The power, controls and water circulation system are all low profile so they can placed under the conveyor. There is no fans to blow over the conveyor to introduce dust.
SST LED system peaks in the wavelength that best fit for the photo-initiator used for white and black screen inks. Traditional UV does not peak in those areas.
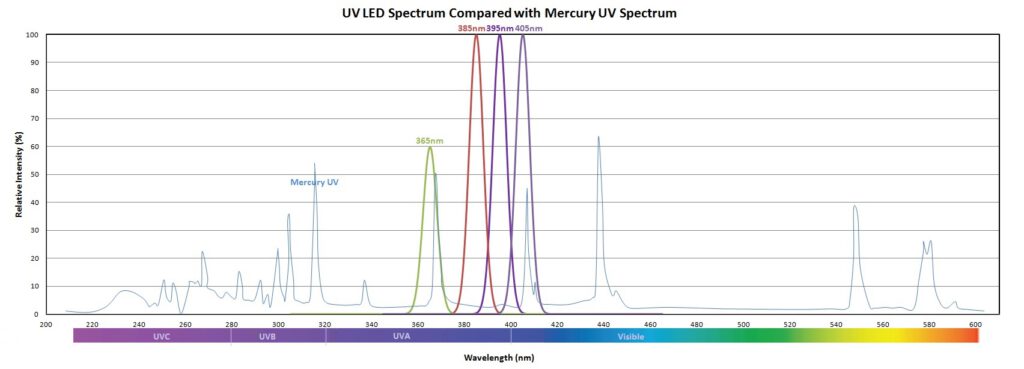
RETROFIT CASE STUDY
The pictures below show the before and after equipment of a typical screen press retrofit from UV to SST LED
This was part of an 11 press retrofit done in 2018 & 2019. The presses ranged from 40 to 60” in width
The equipment on the left (UV Power supply, UV lamp, exhaust blower and exhaust ducting), was completely replaced by the power supply, water circulation and curing lamp the right
The retrofit took approx. 4 hours per press to install
The energy cost to run these presses and exhaust systems were reduced from $73K per year to $5K per year The carbon emissions were reduced from 656 tons per year to 54.
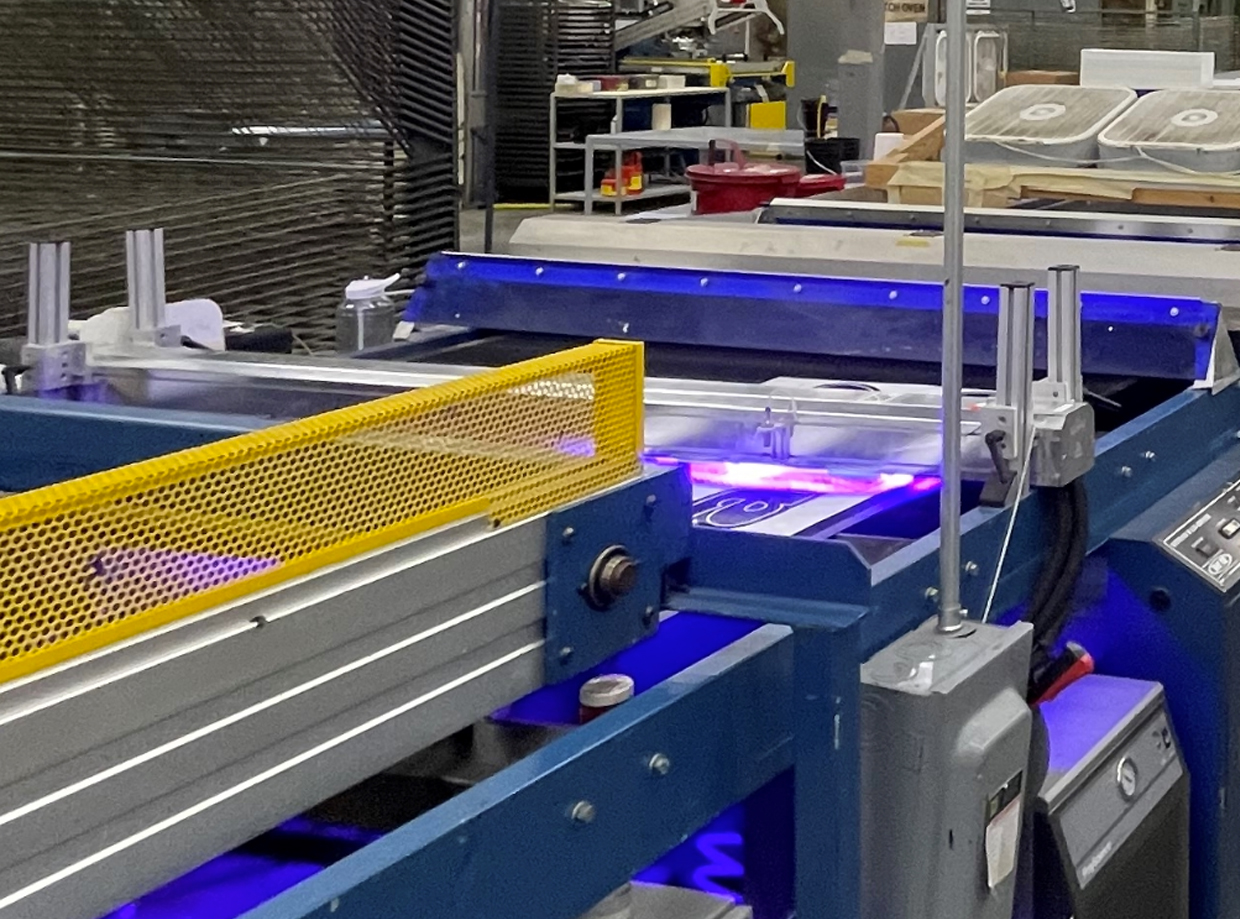
Customized Solutions?
Call (785) 856-0219